Anyone interested in "drop spindle" uprights?
#1
Anyone interested in "drop spindle" uprights?
Anyone interested in a billet steel/cast iron OEM replacement upright that corrects the suspension geometry that results in lowering the car 2" or so? I'm thinking of making a set of 4 for myself... curious if anyone wants to share the cost of getting them made and get a set for themselves.
#2
Evolved Member
iTrader: (21)
This modification would likely not be legal for SCCA Solo SM which is one of the rules I am trying to keep my car compliant with. Granted, SCCA Solo rules are dumb and I am leaning towards just ignoring them anyway as I don't AutoX anymore.
I already have Nagisa arms but could use a little more geometry me thinks as I am down at the 6.5" to the pinch weld in front. I have 1.5" between the bottom of my nut on the Nagisa arm and my wheel so the suspension pickup bracket can't be more than 1.5" lower than stock (1" preferably for debris and wheel balancing weights). I really only need ~0.75" for my arms to be back to parallel.
How much lighter than stock are you aiming?
I'm lazy at comparing the geometric roll center to the center of gravity. Do you have calculations for tthe Evo or anything off the top of your head?
I may be interested in this once in a lifetime opportunity... but I need to know what it will cost.
I already have Nagisa arms but could use a little more geometry me thinks as I am down at the 6.5" to the pinch weld in front. I have 1.5" between the bottom of my nut on the Nagisa arm and my wheel so the suspension pickup bracket can't be more than 1.5" lower than stock (1" preferably for debris and wheel balancing weights). I really only need ~0.75" for my arms to be back to parallel.
How much lighter than stock are you aiming?
I'm lazy at comparing the geometric roll center to the center of gravity. Do you have calculations for tthe Evo or anything off the top of your head?
I may be interested in this once in a lifetime opportunity... but I need to know what it will cost.
Last edited by nollij; Oct 15, 2014 at 08:10 PM.
#3
Evolved Member
iTrader: (8)
The suspension is completely open in street mod other than requiring OEM mounting points. They would be legal.
I've come around more to the idea of an OEM replacement. I would modify a few things geometry wise that would be advantageous for most users though. They can't be drop spindles though, you'll find the front axle is as high as possible already. All you can really do up front is lower the balljoint to raise the roll center. In the back, you might be able to move the axle up though.
Fabricated steel or billet aluminum would be my suggestion.
I've come around more to the idea of an OEM replacement. I would modify a few things geometry wise that would be advantageous for most users though. They can't be drop spindles though, you'll find the front axle is as high as possible already. All you can really do up front is lower the balljoint to raise the roll center. In the back, you might be able to move the axle up though.
Fabricated steel or billet aluminum would be my suggestion.
Last edited by 03whitegsr; Oct 17, 2014 at 11:05 AM.
#5
Evolved Member
I want some, but i have an X. How difficult would it be to model some up for the X?? Oh, and if we could somehow slim out the profile around the center of the hub to fit some proper brake cooling in there, tha'd be grreeeaaattt
#6
EvoM Guru
iTrader: (1)
what would the cost be?
#7
Evolved Member
Seriously though i've got a pretty badass track setup on my X and i track it 12 times a year, so if we make one for the X my evo would make hte perfect test subject.
Trending Topics
#9
I'm working on designs for a set of 6061 hubs that move the lower mount and steering arm down about 1.5-2". Moving the hub bearing assy up 2" isn't feasible with the strut to axle clearance but this will give the same effects on roll center correction.
I don't know if I'll make multiple sets right away though, this is a suspension component and will need to be tested before I'd be comfortable letting others run it. I'll also be making the first sets on a slightly larger bench mill (Novakon torus) that I'm upgrading to but if I made samples to sell I would have a local shop I use for work prototypes make them.
My design is also multi-piece since I don't want to hog out 6" thick aluminum blocks. So the strut mount and steering arms are bolt-on.
I don't know if I'll make multiple sets right away though, this is a suspension component and will need to be tested before I'd be comfortable letting others run it. I'll also be making the first sets on a slightly larger bench mill (Novakon torus) that I'm upgrading to but if I made samples to sell I would have a local shop I use for work prototypes make them.
My design is also multi-piece since I don't want to hog out 6" thick aluminum blocks. So the strut mount and steering arms are bolt-on.
#10
EvoM Guru
iTrader: (1)
I'm working on designs for a set of 6061 hubs that move the lower mount and steering arm down about 1.5-2". Moving the hub bearing assy up 2" isn't feasible with the strut to axle clearance but this will give the same effects on roll center correction.
I don't know if I'll make multiple sets right away though, this is a suspension component and will need to be tested before I'd be comfortable letting others run it. I'll also be making the first sets on a slightly larger bench mill (Novakon torus) that I'm upgrading to but if I made samples to sell I would have a local shop I use for work prototypes make them.
My design is also multi-piece since I don't want to hog out 6" thick aluminum blocks. So the strut mount and steering arms are bolt-on.
I don't know if I'll make multiple sets right away though, this is a suspension component and will need to be tested before I'd be comfortable letting others run it. I'll also be making the first sets on a slightly larger bench mill (Novakon torus) that I'm upgrading to but if I made samples to sell I would have a local shop I use for work prototypes make them.
My design is also multi-piece since I don't want to hog out 6" thick aluminum blocks. So the strut mount and steering arms are bolt-on.
It's been proven in off road racing where upper contol arms have been made of billet aluminum that fabricated chromoly ones are stronger and lighter..
I would machine the hub block and caliper mount as one piece. Machine the balljoint mount as a separate piece that gets welded to the hub block. The steering arm can be fabbed with 12 gauge chromoly, replace the outer tierod with a hiem. The strut mount can also be machined separately, but fairly small, and welded to the hub block with 12 gauge gussets...
The spindle on my ranger, for example, weighs 9lbs with out the snout and 1" uniball in it. Its a 3/4" thick chunk of mild steel machined to fit the dana 44 snout, 1/4" think caliper bracket welded on, a 1.25" .120 wall chromolly tube runnin from the snout block up to the uniball cup. Boxed in with 12 gauge chromolly. The steering arm is 12 gauge chromolly with weld washers. The upper arm is 1.5" .095 chromolly tube, the uniball capture is 12 gauge chromolly. You can fold the arm in half by hand if its not bolted to a uniball, it weighs 2lbs. The lower arm is heavy so it survives hitting rocks. Those light weigh bits hold a 35" tall 100lb wheel/tire on to a 3900lb truck that goes 75mph+ through the rough in the desert.
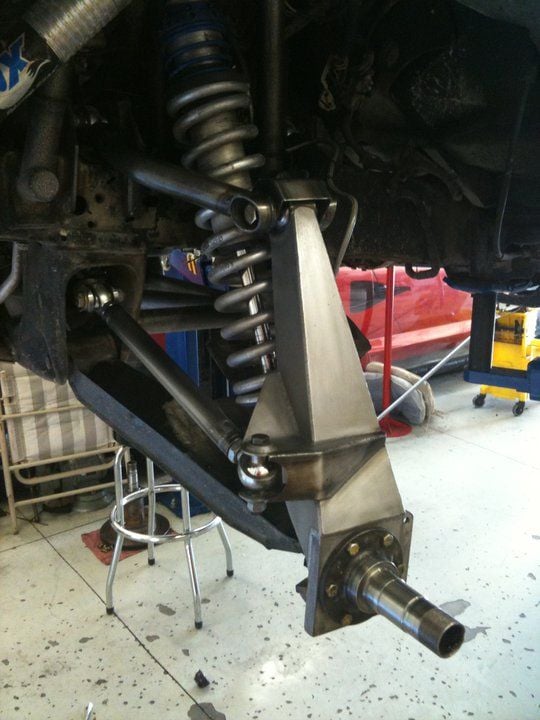
My point is, you can make those spindles a whole hell of a lot lighter than you probably think you can. The Jet Black Racing team had their billet spindles at Road Race's booth at MOD, and they look over built by a lot IMO..
#11
Ive thought about sheet metal since I do a lot of sheet metal design at work but there are several issues against it. One is the use of factory lower control arm and ball joint (or whiteline since an OEM replacement isn't available). Another is just the overall space compared to what you have in the wheelers.
Billet works for tight areas when small geometries are needed and you're not likely to find much other than billet steel or aluminum in track/rally car hubs.
Heat is also an issue with aluminum if you build it up but in reality he dissipation is high in that area and aluminum is common in race cars for hubs. I do worry about the heat and possibly ruining the T6 temper so Ill have to measure temps to see what builds up.
Billet works for tight areas when small geometries are needed and you're not likely to find much other than billet steel or aluminum in track/rally car hubs.
Heat is also an issue with aluminum if you build it up but in reality he dissipation is high in that area and aluminum is common in race cars for hubs. I do worry about the heat and possibly ruining the T6 temper so Ill have to measure temps to see what builds up.
#12
EvoM Guru
iTrader: (1)
Anyone interested in "drop spindle" uprights?
I said to use a billet piece for the hub block, caliper bracket, and lower arm piece.
The steering arm and strut attachment don't need to be solid, and could be lighter if properly fabricated.
And idk what space you're talking about, my truck had 15" wheels on it when those uprights were designed...
The steering arm and strut attachment don't need to be solid, and could be lighter if properly fabricated.
And idk what space you're talking about, my truck had 15" wheels on it when those uprights were designed...
#13
Evolved Member
Sheet metal steel hubs work well. They're cheap and easy to make if you know how to weld. They HAVE to be made out of 4130 or stronger metal though. This is definately a good plausible solution.
Yes, billet aluminum ones will be lighter. Do not use 6061. Use 7075. I wouldn't worry about 7075 loosing its temper, but 6061 is too flexible for something like a hub.
The other gentleman is right, Chromoly tubing is much better than aluminum tubing in places where there is ONLY tension or compression. The tubing can be smaller, giving us clearance where we need it.
Dallas, i have an X, but if this can be fitted on an X i'd love to be a test mule for you. If you have a design in CAD or something i can see if i can stick it in COSMOS or ANSYS for you. I haven't used those programs or designed an upright since my FSAE days, but i'm sure i can figure it out all over again
As far as the steering arm linkage, make it adjustable. You'll likely find you need to tweak it a bit to perfect your bump-toe. After you find out what is optimal, make it fixed for kits you sell. If you could also increase the Ackerman ratio on steering geometry, i would buy you 10 kegs of beer.
Yes, billet aluminum ones will be lighter. Do not use 6061. Use 7075. I wouldn't worry about 7075 loosing its temper, but 6061 is too flexible for something like a hub.
The other gentleman is right, Chromoly tubing is much better than aluminum tubing in places where there is ONLY tension or compression. The tubing can be smaller, giving us clearance where we need it.
Dallas, i have an X, but if this can be fitted on an X i'd love to be a test mule for you. If you have a design in CAD or something i can see if i can stick it in COSMOS or ANSYS for you. I haven't used those programs or designed an upright since my FSAE days, but i'm sure i can figure it out all over again

As far as the steering arm linkage, make it adjustable. You'll likely find you need to tweak it a bit to perfect your bump-toe. After you find out what is optimal, make it fixed for kits you sell. If you could also increase the Ackerman ratio on steering geometry, i would buy you 10 kegs of beer.
#14
I had some ideas last night about how to make the sheet metal work with a machined hub mount/brake mount and machined lower ball joint mount. I'll probably go through the design process in both sheet metal and aluminum and decide which way I like better.
I don't know if it will work on an X or not but I'll be working with English Racing to distribute if they turn out sellable, so if small changes are needed that shouldn't be an issue.
Since I'm working on these alone for my own little LLC to help support my racing, I'll need to do a design review and will probably make a thread and let my fellow EvoM engineers provide input instead of designing in a vacuum. I thought I would be further along than I am with this by now but a baby threw a wrench in things so expect some updates this winter when racing season ends.
I don't know if it will work on an X or not but I'll be working with English Racing to distribute if they turn out sellable, so if small changes are needed that shouldn't be an issue.
Since I'm working on these alone for my own little LLC to help support my racing, I'll need to do a design review and will probably make a thread and let my fellow EvoM engineers provide input instead of designing in a vacuum. I thought I would be further along than I am with this by now but a baby threw a wrench in things so expect some updates this winter when racing season ends.
#15
Evolved Member
iTrader: (8)
2. 7075 has a lower KIC then 6061 which means it actually more likely to fail in fatigue then 6061.
3. 7075 suffers from SCC.
If you want high strength aluminum, use 2024 or if you are truly designing for minimum weight, 7050. Both would be an absolute waste here though. They are harder to machine, cost a lot more, and this is a stiffness based design anyway, not strength based. Going to stronger aluminum will do absolutely nothing for you.
As far as the steering arm linkage, make it adjustable. You'll likely find you need to tweak it a bit to perfect your bump-toe. After you find out what is optimal, make it fixed for kits you sell. If you could also increase the Ackerman ratio on steering geometry, i would buy you 10 kegs of beer. How To Calculate & Measure Bump Steer | BestTireAndWheelShop.com - YouTube
Just my $0.02, I'd do a fabricated sheet steel piece. Bend up a single thicker piece that would make up the hub mount, caliper mount, one side of the strut mount and one side of the steering arm. Tube ring around the axle and box into the ring for everything else. You'd need to have decent bends on the front piece to ensure correct positioning but everything would be pretty straight forward. Change to a rod end in double shear on the tie rod and leave space so you can adjust it up/down to correct bump steer. Keep the same steering ratio and ackerman. Match the brake caliper mount to stock so any aftermarket BBKs work the same way. Design your LCA weld joint and machined block so you could fixture it in two positions. One for 17" wheels, one for 18" wheels and make the tie-rod adjustment range cover both.