Anyone interested in "drop spindle" uprights?
#16
Evolved Member
1) 7075 is definately stiffer than 6061. Only by about 400 ksi, but it also plasticly deforms more and has less chances of catastrophic faliure. When stiffness is a main concern, no one bothers with 6061 unless they're budget limited.
2) I've never seen a 7 series aluminum fail in cyclical fatigue that wasn't on an airplane traversing the sonic barrier. So as long as you remain subsonic, a 7 series is fine. (sarcasm intended)
3) Stress corrosion cracking? Never heard of such a thing on a racecar. And i don't know a single purpose built open wheel racecar that doesn't use aluminum uprights (rules permitting). All the FSAE cars i knew of either ran steel sheet metal uprights or 7075 cnc'd uprights. The winning teams were usually on 7075, though that is more a sign of better funding than better performance.
Never worked with 2 series aluminum so i can't share any experience there.
As far as ackerman goes, 120% usually feels pretty good. Not sure how much is on the evo stock. BMW E46 front suspension geometry is pretty darn awesome so you might be able to steal a bunch of stuff if you have one modeled up.
+1 to all the other stuff whitegsr said
2) I've never seen a 7 series aluminum fail in cyclical fatigue that wasn't on an airplane traversing the sonic barrier. So as long as you remain subsonic, a 7 series is fine. (sarcasm intended)
3) Stress corrosion cracking? Never heard of such a thing on a racecar. And i don't know a single purpose built open wheel racecar that doesn't use aluminum uprights (rules permitting). All the FSAE cars i knew of either ran steel sheet metal uprights or 7075 cnc'd uprights. The winning teams were usually on 7075, though that is more a sign of better funding than better performance.
Never worked with 2 series aluminum so i can't share any experience there.
As far as ackerman goes, 120% usually feels pretty good. Not sure how much is on the evo stock. BMW E46 front suspension geometry is pretty darn awesome so you might be able to steal a bunch of stuff if you have one modeled up.
+1 to all the other stuff whitegsr said
#18
Evolved Member
iTrader: (8)
400ksi is 3%...which is within the realms of measurement error and statistical variance here. It's >90% aluminum in both cases and the base metal dictates the stiffness almost exclusively since elasticity happens at the atomic level, not the grain level where 7075 is different then 6061. 7075 is cleaner though so I could seeing it having a SLIGHT edge here over 6061. But at 2X the price is it really worth that 3% bump in stiffness?
7075 has an elongation at break of 11% though and 6061 is 12%. Technically, 6061 undergoes more plastic deformation before fracture than 7075...but again, it's so close it really doesn't matter.

From a damage tolerant design perspective, 6061-T6 has a KIC T-L of 29.0MPa-m1/2 where 7075-T6 has a KIC T-L of 25.0MPa-m1/2. For a given design, once a crack nucleates, the 6061 will actually have a slower crack growth rate than 7075. Despite 7075 being considerably stronger in yield and ultimate strength. The important thing to identify here is EVERY PART has crack nucleation sites. It can be as simple as a scratch or bad tool path.
3) Stress corrosion cracking? Never heard of such a thing on a racecar. And i don't know a single purpose built open wheel racecar that doesn't use aluminum uprights (rules permitting). All the FSAE cars i knew of either ran steel sheet metal uprights or 7075 cnc'd uprights. The winning teams were usually on 7075, though that is more a sign of better funding than better performance.
Code:
Material Yield Ultimate KIC 2024-T3 393MPa 496MPa 32.0MPa-m1/2 6061-T6 276MPa 310MPa 29.0MPa-m1/2 7075-T6 503MPa 572MPa 25.0MPa-m1/2 7050-T76 490MPa 552MPa 31.0MPa-m1/2
As far as ackerman goes, 120% usually feels pretty good. Not sure how much is on the evo stock. BMW E46 front suspension geometry is pretty darn awesome so you might be able to steal a bunch of stuff if you have one modeled up.
+1 to all the other stuff whitegsr said
+1 to all the other stuff whitegsr said
Last edited by 03whitegsr; Aug 27, 2015 at 04:45 PM.
#19
EvoM Guru
iTrader: (1)
Damn engineers with your math...
#21
Evolved Member
Yup, 4 different cars. The best performing suspension on all of them were the 2 cars pictured in pics #2, 4 & 5. The failed suspension was because we had a balljoint in shear, unbeknownst to us. We tended to have issues where certain rod ends were in shear when we had originally designed them to be in pure tension/compression. Just goes to show how imperative accurate welding, machining, and assembly is. We tried many things like pull,push, inline rockers, counter rockers, and my experience tells me that it doesn't really matter. Whatever you need to do to make your packaging work and make working on the car as easy as possible. One of the best aspects of our car was that it was VERY easy to work on. Everything was within reach and could easily be torn down and put back together in a hurry.
Those were the days
Those were the days

#22
Evolved Member
First, I misjudge your response. I figured you were just coming from the marketing hype mentality and thought "7075 is always superior." My apologies. I would like to discuss further though.
400ksi is 3%...which is within the realms of measurement error and statistical variance here. It's >90% aluminum in both cases and the base metal dictates the stiffness almost exclusively since elasticity happens at the atomic level, not the grain level where 7075 is different then 6061. 7075 is cleaner though so I could seeing it having a SLIGHT edge here over 6061. But at 2X the price is it really worth that 3% bump in stiffness?
7075 has an elongation at break of 11% though and 6061 is 12%. Technically, 6061 undergoes more plastic deformation before fracture than 7075...but again, it's so close it really doesn't matter.
I can show you LOTS of examples of 7075 failing below supersonic speeds, as speeds don't dictate structural loads. Sure, higher air speeds induce higher loads, but I could cyclically fatigue a piece of aluminum moving about 1/2" a second.
But that's besides the point.
From a damage tolerant design perspective, 6061-T6 has a KIC T-L of 29.0MPa-m1/2 where 7075-T6 has a KIC T-L of 25.0MPa-m1/2. For a given design, once a crack nucleates, the 6061 will actually have a slower crack growth rate than 7075. Despite 7075 being considerably stronger in yield and ultimate strength. The important thing to identify here is EVERY PART has crack nucleation sites. It can be as simple as a scratch or bad tool path.
SCC can take place in all machined 7075 parts that aren't stress relieved after machining. The residual stress from machining alone can cause cracking in the component as it sits on a shelf waiting to be used.
2024 falls between 6061 and 7075 on price and machinability. As you can see though, it has nearly the strength of 7075 but WAY BETTER fracture toughness. Or if you want the strength of 7075 and the fracture toughness of 2024, find some 7050-T76. I believe it's more expensive then 7075 though.
I'll look when I get a chance and post up the ackerman numbers. Seems like at around 35* steering angle it was about 6* of ackerman, but I could be wrong. Not sure how the curves would really compare though either.
400ksi is 3%...which is within the realms of measurement error and statistical variance here. It's >90% aluminum in both cases and the base metal dictates the stiffness almost exclusively since elasticity happens at the atomic level, not the grain level where 7075 is different then 6061. 7075 is cleaner though so I could seeing it having a SLIGHT edge here over 6061. But at 2X the price is it really worth that 3% bump in stiffness?
7075 has an elongation at break of 11% though and 6061 is 12%. Technically, 6061 undergoes more plastic deformation before fracture than 7075...but again, it's so close it really doesn't matter.
I can show you LOTS of examples of 7075 failing below supersonic speeds, as speeds don't dictate structural loads. Sure, higher air speeds induce higher loads, but I could cyclically fatigue a piece of aluminum moving about 1/2" a second.

From a damage tolerant design perspective, 6061-T6 has a KIC T-L of 29.0MPa-m1/2 where 7075-T6 has a KIC T-L of 25.0MPa-m1/2. For a given design, once a crack nucleates, the 6061 will actually have a slower crack growth rate than 7075. Despite 7075 being considerably stronger in yield and ultimate strength. The important thing to identify here is EVERY PART has crack nucleation sites. It can be as simple as a scratch or bad tool path.
SCC can take place in all machined 7075 parts that aren't stress relieved after machining. The residual stress from machining alone can cause cracking in the component as it sits on a shelf waiting to be used.
Code:
Material Yield Ultimate KIC 2024-T3 496MPa 393MPa 32.0MPa-m1/2 6061-T6 276MPa 310MPa 29.0MPa-m1/2 7075-T6 503MPa 572MPa 25.0MPa-m1/2 7050-T76 490MPa 552MPa 31.0MPa-m1/2
I'll look when I get a chance and post up the ackerman numbers. Seems like at around 35* steering angle it was about 6* of ackerman, but I could be wrong. Not sure how the curves would really compare though either.
Thx for the counter info. I don't have a whole ton of exp with those grades of aluminum. Is 3% worth twice the price? Nah, probably not. But you know, that doesn't matter because racecar. I think when it comes to the hub, one material property that would be more important to look at is fatigue strength with respect to temperature. A steel design wins here handsdown, and i don't really know how hot the hub can get in a track situation, so this might require some actual engineering.
I've honestly never seen aluminum fail from fatigue but then again, i don't deal with high cyclical stuff. The 6061vs7075 comparison in fatigue is just stuff i heard from aerospace guys.
#23
Evolved Member
#24
EvoM Guru
iTrader: (1)
The spindle itself doesn't get that hot. The hub does, but not the spindle. Cars come in and you can't even hold the lug nuts with a mechanix glove on, but you can grab the spindle bare handed.
#25
Evolved Member
iTrader: (8)
Reality is though, I'm selling my car when I get it together so it's not something I'm pursuing any more.
#26
Evolved Member
iTrader: (34)
I'd be happy enough if someone made sheet metal hubs/spindles with appropriate relocation to allow more drop. As long as it's same weight/not much heavier than the OEM solid chunk of iron, sheet metal should be way cheaper and achieve what the masses want.
The engineers can continue to nerd out on aluminum alloys and CNCing and Ackerman angles while the rest of us get to slam our rides to the deck and run around the track
. Seriously though it would be useful not to trade suspension geometry for better aero/down force with cars running splitters and diffusers.
The engineers can continue to nerd out on aluminum alloys and CNCing and Ackerman angles while the rest of us get to slam our rides to the deck and run around the track

#27
Evolved Member
I'll just leave this thread right here...... Hands down the best thread in all of the internet.
http://www.gtrlife.com/forums/topic/.../page__st__140
http://www.gtrlife.com/forums/topic/.../page__st__140
#28
Evolved Member
iTrader: (8)
Here is the calculated Ackermann in percentage of outside tire steering angle at the wheel.
It more closely matches a heavily modified suspension:
Offset PSRS
Whiteline RCK
Whiteline PSK
20mm wheel spacer and max negative camber at the knuckle
Camber plates setup to max out caster (no camber from them)
EDIT: Corrected the chart
It more closely matches a heavily modified suspension:
Offset PSRS
Whiteline RCK
Whiteline PSK
20mm wheel spacer and max negative camber at the knuckle
Camber plates setup to max out caster (no camber from them)
EDIT: Corrected the chart
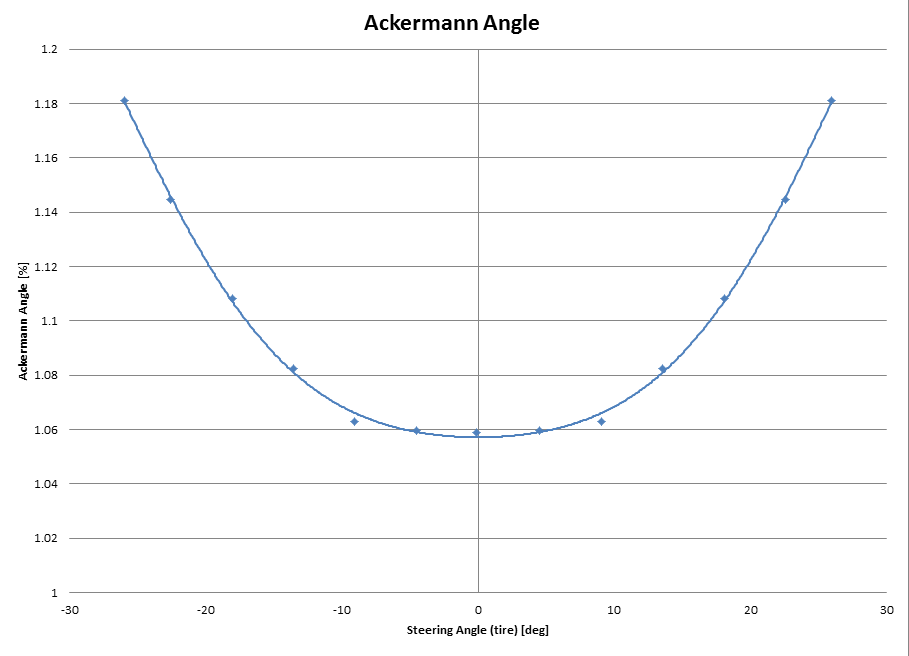
Last edited by 03whitegsr; Aug 21, 2015 at 09:02 PM.
#29
Evolved Member
Interesting! So we're getting about 118% at 30 deg. That's a bit more than what i was expecting. I'd be willing to bet that the compliance in the bushings reduces that, which makes sense as to why i had a hunch of 110% ackerman stock.
What was your setup/method of measurement? I'd like to see how you did this as i was wanting to get bump/toe curves for the front/rear as well as the camber curves. Unless you want to do that
What was your setup/method of measurement? I'd like to see how you did this as i was wanting to get bump/toe curves for the front/rear as well as the camber curves. Unless you want to do that

#30
Evolved Member
iTrader: (8)
Like I said, it reflects a fairly modified suspension. Basically all the off-the-shelf parts you can get for the car. How much it has stock, I don't know. Bushing compliance though wouldn't be a concern here, it had spherical bearings in all the pivots and the EVO subframe doesn't have any bushings on it connecting it to the unibody.
Measured all the arms while they were off the car so I could make accurate solid models. Used a water level and bob-weight to measure the chassis points. Measured twice, had 1/32" repeatability and figured it was good enough.
Measured all the arms while they were off the car so I could make accurate solid models. Used a water level and bob-weight to measure the chassis points. Measured twice, had 1/32" repeatability and figured it was good enough.